导读:近年中国金属基超硬材料制品行业技术水平及发展趋势。金属基超硬材料制品行业技术水平的核心是不断研发新配方、新工艺,以促进超硬材料制品在相关产业中的应用。
参考《2016-2022年中国等离子切割机行业竞争现状及十三五投资战略分析报告》
金属基超硬材料制品行业技术水平的核心是不断研发新配方、新工艺,以促进超硬材料制品在相关产业中的应用。在硬脆材料加工领域,随着被加工对象的多样化和加工难度的提高,各种前沿新技术正在被高度关注与重点研发,部分已逐步得到应用。这些技术中,金刚石表面处理技术有效增加了胎体对磨料的把持力,提高了金刚石的利用率;超细金刚石有序排布技术有效改善了磨粒分布状态,可以成倍提高金刚石工具的生产效率和使用寿命;预合金粉末和改性材料的应用可有效改善胎体性能;无压烧结技术可显著提高产品烧结质量,降低烧结能耗;激光焊接技术能够保证较高的焊接强度,且可实现无水切割,满足用户对安全、环保、施工条件等多方面的综合要求。
但是,目前我国的超硬材料制品行业的整体技术与质量水平仍落后于意大利、日本等发达国家。虽然近年来奔朗新材、博深工具和本公司等少数几家超硬材料制品企业脱颖而出,逐步掌握了用于传统硬脆材料加工的金属基超硬材料制品的先进生产技术,但我国超硬材料制品企业发展极不平衡,低端生产企业数量众多且规模相对较小,大多数低端超硬材料制品生产企业缺乏自主研发设计能力,仍然采用单质金属粉末、手工称料装料等低水平的生产技术和加工工艺,导致其产品质量和使用性能低下。特别是我国用于生产超硬材料制品的金属粉末胎体材料的制备技术及应用与发达国家存在差距。根据中国超硬材料网2011年发表的《超硬材料制品未来两年市场发展及行业展望》,在超硬材料制品生产过程中,发达国家约有60%的超硬材料制品采用预合金粉作为胎体材料,而我国采用预合金粉做为胎体材料的超硬材料制品不到10%,大多数超硬材料制品生产企业仍采用单质粉作为胎体材料。
各种新技术的不断开发和使用,符合现代加工技术高效率、低消耗的环保理念,也是基础工业飞速发展的的实际需求。就硬脆材料加工用超硬材料制品而言,新材料、新技术、新工艺将不断涌现和推广应用,促进了超硬材料制品技术的升级,使超硬材料制品性能不断提升并保持了活力。未来,金属基超硬材料制品行业的主要技术发展趋势如下:
① 金刚石工具用超细预合金粉末的应用
金属基超硬材料制品性能优劣的关键在于金属粉末烧结体对超硬磨粒的把持力及烧结体与磨粒间的磨损适配性,而金属粉末烧结体的性能主要取决于金属粉末颗粒间相互作用时的合金化程度。目前,国内多数生产企业的配方体系中以较粗的单质元素粉料为成分主体。尽管采用单质粉进行生产在配方调节的灵活性和易于成型的方面优势明显,但是金属粉末颗粒之间属于表层部分合金化,导致胎体强度较低,对金刚石的包镶效果差,且刀齿胎体容易产生成份偏析。此外,完成单质元素粉末合金化过程需要足够的温度和较长的时间,能源消耗较大,导致产品的经济效益较低。
随着市场竞争的日益激烈和对产品性能要求的提升,有关胎体粉末的研究受到行业内的广泛关注,预合金粉的研发和应用将在行业中取得了较好的反响。预合金粉是指按照特定的成分配比,通过雾化、机械破碎或化学方法将金属制成特定粒度的合金粉末。与单质粉相比,预合金粉具有合金化成分均匀、成形性好、烧结体致密程度高等特点。采用预合金粉作胎体生产的金刚石工具,具有生产效率高、衰减慢的特点。目前,国内仅有少数企业采用预合金粉进行生产,预计未来几年将逐渐占据主导地位。
近年来,以有研粉末新材料(北京)有限公司和发行人为代表的行业领先企业,凭借较为领先的研发优势,掌握了金刚石工具用超细预合金粉的制备技术。
与传统预合金粉相比,超细预合金粉的粒度更细,具有比表面积大、粉末活性强等特点,能够以较低的烧结温度和较短的烧结时间,获得较高的烧结硬度,产品具有把持性好、锋利度高、耐磨性强、能耗小等特点。超细预合金粉是目前世界范围内最为先进的金属基金刚石工具的胎体制备材料,将成为金刚石工具领域的未来发展趋势。
② 金刚石表面处理工艺
金刚石工具的寿命和使用效率除了与胎体材料和磨料的性能有关外,还取决于二者之间的结合强度。由于金刚石磨料与一般金属的粘结能力较差,与金属基胎体材料之间无界面结合力,仅靠胎体对磨料的机械镶嵌作用,在使用过程中磨粒易出现脱落,导致金刚石工具使用寿命短且工作效率低。金刚石表面处理技术的应用,使金刚石表面具有了金属本身的特性,从而增强了金刚石与金属胎体之间结合力,大幅提高了金刚石工具的切削性能和使用寿命。随着金刚石工具应用日益广泛,对其应用指标和性能要求也越来越高,化学沉积、真空沉积等各种表面处理技术与方法应运而生。在众多表面处理技术中,目前真空微蒸发沉积技术在金属基超硬材料制品实际生产中得到了较为广泛的应用,但是该技术应用成本较高。未来,具有成本低、适用性广、性能好、实用性强等特点的金刚石表面处理工艺将成为行业技术的发展方向。
③ 金刚石有序排列技术
传统金刚石工具胎体中的金刚石是随机分布、无序排列的,容易产生偏析与聚集,造成金刚石工具生产效率低、使用寿命短。采用金刚石有序排列(多层、均布金刚石)技术,使每粒金刚石都得到充分的利用,克服了采用机械混料工艺带来的金刚石分布不均严重影响到切割性能的缺陷,能够显著提高金刚石工具的生产效率和使用寿命,同时提升加工对象的光洁度,减少金刚石重复磨损,是当今世界生产金刚石工具的最新技术。
④ 自动冷压及制粒工艺
建筑陶瓷用金刚石工具刀头自动冷压技术近几年才开始推广应用。自动冷压技术可以提高刀头单次热压数量和烧结质量,从而提高冷压效率,降低物料消耗和人工成本。通过冷压后烧结,单模产量可提高约一倍,电耗可降低约 40%,物料消耗可降低约 30%,产品质量也因单重误差减小而更加稳定。
制粒工艺是实现较大尺寸金刚石刀头高效自动冷压的重要环节,在国外已被广泛应用。“制粒”又叫“造粒”,是把粉末、熔融液、水溶液等状态的物料经加工制成具有一定形状与大小粒状物的过程,是为了改善粉末流动性而使较细颗粒团聚成粗粉团粒的一种工艺。目前的金刚石工具生产中广泛采用湿法制粒技术,通过将熔融金属通过小孔或筛网自动地注入空气或水中,冷凝后便得到金属粉末,该法得到的粉末粒度较粗,一般可以达到 0.5~1mm,适于制取较低熔点金属粉末。通过制粒技术的成功应用,可以改善粉末流动性,防止金刚石颗粒和超细粒度粉末如钴、镍等成分的偏聚,防止粉尘扩散及在器壁上的黏附,有效提高金刚石制品的尺寸与重量精度,改善金刚石刀头生产中压力的均匀传递。随着我国金刚石工具行业技术的发展,制粒工艺作为一项重要的技术将被广泛应用于建筑陶瓷用金刚石工具刀头生产过程中,但目前尚存在制粒成本较高的难题有待解决。
⑤ 采用先进节能的烧结工艺
烧结是金属基超硬材料制品制造过程中最关键的工序之一,也是能源消耗的最主要环节,烧结过程的能耗占超硬材料制品生产能耗的 70%以上。目前,行业内最常用的烧结方式是以低电压、大电流为特征的热压烧结,这种烧结方式具有烧结时间短、烧结温度低、适用范围广、工艺调整灵活等优势,但是生产过程中能耗较大,产品稳定性较差。
目前,冷压烧结技术等前沿烧结新技术在西方发达国家被高度关注与重点发展,并不同程度地应用于金刚石工具制造过程,显著提高产品烧结质量,降低烧结能耗,是烧结技术的发展方向。其中,无压烧结在达到较好的致密化效果的同时,保证烧结毛坯的形状及尺寸精度,最大限度地减少烧结后的磨削加工余量,而且烧结过程中能耗低,适合于规模化生产。该技术在美国、日本、德国等工业发达国家已经被普遍采用。未来,随着行业先进生产设备的不断开发和应用,以及国家节能减排政策的大力推行,上述具有节能降耗、烧结质量稳定、生产效率高等优势的烧结工艺将被广泛采用。
⑥ 更加安全的激光焊接工艺
目前,我国硬脆材料加工用金刚石工具的焊接仍以高频焊接为主。高频焊接是通过高温熔化介质将刀头与基体焊接在一起的焊接工艺,且大多采用手工焊接,焊缝的结合强度不够高,产品安全性较低,产品的尺寸精度及焊接质量的一致性无法保证。因此,采用高频焊接工艺生产的产品很难达到精度高、切削速度快、使用寿命长等较高的性能要求,只能满足通用市场的产品需求。
随着生产条件的改善和对产品性能要求的提升,具有焊接强度高、自动化程度高、生产效率高等优点的激光焊接成为了本行业焊接工艺的发展方向。激光焊接是以聚焦的激光束作为能量,熔化刀头的过渡层与基体,形成牢固的焊缝,能够保证很高的焊接强度,确保使用的安全性。激光焊接技术目前是世界上最先进的硬脆材料加工用超硬材料制品的焊接技术,在发达国家已普遍使用,未来具有极大的发展潜力。
资料来源:公开资料,报告网整理,转载请注明出处(YS)。
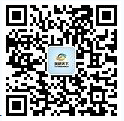
【版权提示】观研报告网倡导尊重与保护知识产权。未经许可,任何人不得复制、转载、或以其他方式使用本网站的内容。如发现本站文章存在版权问题,烦请提供版权疑问、身份证明、版权证明、联系方式等发邮件至kf@chinabaogao.com,我们将及时沟通与处理。