改革开放30年,人们物质生活得到极大丰富。
从一票难求的“的确良”到色彩斑斓的时装,从12英寸黑白电视的简陋外观到液晶电视的精美外壳,从价格低廉的家居塑料用品到高科技化工材料制作的高档家具,这些变化,都与一种被称为乙烯的化工原料紧密相关。
乙烯,被称为“石化工业之母”,是石油化工基础性原料。
20世纪70年代后期,美国的乙烯产能已达2000万吨,而当时的中国,乙烯年生产能力仅为6万吨。
在艰难中起步的中国乙烯产业,在改革开放后得到迅速发展。2008年,全国乙烯产能已近1000万吨,居世界第二位。其中,有600多万吨来自中国石化。
中国石化,作为国有特大型能源化工企业,已跃居世界第五大乙烯生产商。
“集中力量办大事”,在乙烯产业发展的道路上,中国石化坚持内涵发展,规模化步伐不断加快。
“1976年,经过毛主席圈阅,周总理批准,我国第一套从日本引进的30万吨/年乙烯装置在我们燕山石化开工建设,在这之前我们国家大概只有几万吨的乙烯装置,标志着我国石油化工大型化的建设开始了新的道路。”燕山石化原副总经理、总工程师杨清雨回忆起当时的情形仍旧充满自豪。
“当时我们把30万吨乙烯建设当做为毛主席争光、为祖国争光的一个政治仗来打,组织全国精兵强将参加装置的开工建设。5月8日,第一次投料成功,那种高兴劲真是难以言表!”
1983年中国石化总公司成立,当时全国的乙烯产能是65.4万吨,中国石化总公司拥有乙烯产能60.64万吨。遵照中央“集中力量办大事”的指示,在中国石化的统一组织下,当时处于暂停建设阶段的4套30万吨/年乙烯工程在大庆石化、齐鲁石化、扬子石化、上海石化恢复建设。
1998年,中国石化集团公司重组成立,当时全国乙烯产能377.2万吨,中国石化的乙烯产能为257.5万吨。
2008年,全国乙烯产能约1000万吨,中国石化产能达到629.5万吨。
“十五”期间,中国石化的乙烯产能增长速度达到年均15.6%,创造了乙烯产业发展中的奇迹。
“在乙烯产能建设中,中国石化坚持科学发展、内涵发展,通过对原有的大型乙烯装置实施两轮改扩建,我们的乙烯产业向规模化发展。”中国石化集团公司发展计划部的有关人员说。
上个世纪90年代初,中国石化按照“大型、先进、系列、集约、深度”的发展战略对五大乙烯装置进行第一轮技术改造。燕山石化是第一轮改造的领头羊,改造完成后,时任国务院副总理的朱镕基批示:“燕山石化乙烯的改造在建设思想、建设模式、建设方法上,有了创造性的发展。”随后,大庆石化、扬子石化、上海石化、齐鲁石化等30万吨乙烯装置的产能先后改造为40万~45万吨。
1998年开始的第二轮技术改造,突出“质量、品种、成本、效益和顶替进口”,先后对燕山石化、上海石化、扬子石化、齐鲁石化、茂名石化等大乙烯进行改造,产能分别达到70万吨至100万吨不等。
“在改造中,中国石化尽可能依托原有装置进行改造,事实证明这条路子是正确的,投资少、多产出、见效快。第二轮改造后,新增生产能力175万吨,平均吨乙烯投资1.4万元,与新建相比,节省投资超过30%。”
在改造现有装置的同时,福建炼化一体化项目、天津石化、镇海炼化等新建百万吨乙烯基地正拔地而起。
“预计到2012年,中国石化集团公司的乙烯产能将达到1070万吨/年。”
改革开放,为中国石化引进先进技术和设备创造了有利条件;同时,公司坚持引进—消化吸收—集成创新—自主创新的发展道路,使中国石化的乙烯产业竞争力不断提升。
“第一套30万吨乙烯装置在燕山石化投产时,整个工艺设备,所有的装备包括一个螺丝钉都是引进的,没有我们中国的一个东西。”杨清雨说。
2006年,当茂名石化百万吨乙烯改造完成时,装置的国产化率达到80%以上,该套装置的核心设备——裂解气压缩机也是由国内自行设计和制造的。
在乙烯产业发展中,中国石化一直坚持“引进—消化吸收—集成创新—自主创新”的发展思路,在关键装备国产化和核心、专有技术研发方面迈出重要步伐。
1988年,首台国产乙烯裂解炉——CBL-I型炉由当时的北京石化工程公司、北京化工研究院和兰州化机院共同研制成功。虽然这台炉子的产能仅为2万吨/年,但这是第一台由我国自主设计生产的裂解炉。它的诞生,改写了我国乙烯装置关键设备全部依靠引进的历史。
2000年9月,中国石化与美国鲁姆斯公司合作开发的10万吨/年的单台液体原料裂解炉(SL-I型炉)投料成功,其整体技术达到国际先进水平。“燕山石化在中外合资合作开发大型裂解炉中第一次吃了螃蟹。”
在茂名石化乙烯改扩建项目中,510台设备中有448台设备由国内制造,大型裂解气压缩机和冷箱等关键设备都是国产的。目前,中国石化乙烯装置的整体国产化率达到70%,通过国产化掌握了一大批具有自主知识产权的设计制造核心技术。
中国石化已经为建设百万吨级规模乙烯装置做好了技术准备,具备了采用自主技术建设百万吨级乙烯装置的能力。
改革开放,打开了我们的国门,也打开了我们的视野。在坚持自主创新的同时,加强对外合作,也使中国石化乙烯装置的管理和技术水平不断得到提升。
1999年10月,江总书记率领代表团访问英国,当时的国家计委在伦敦宣布,中国石化、上海石化与BP公司合资建设上海赛科90万吨乙烯项目建议书已得到批准,厂址选在上海化学工业区内。
1999年11月,中国石化与德国巴斯夫合资建设南京扬巴一体化项目的可研报告协议签字仪式在北京举行,朱镕基总理和来访的施罗德总理出席仪式。2001年9月28日的开工典礼上,中国石化第一任总经理、时任全国政协副主席的陈锦华按下了开工按钮,打下了第一根桩。
2005年3月,上海赛科90万吨乙烯装置建成投产。同年5月,扬巴60万吨乙烯装置顺利开车。
这些合资项目的建设采用国际通行的项目管理和建设模式,保证了项目建设安全、质量、投资、进度和合同得到控制;采用成熟可靠的先进技术,使各装置能耗物耗均处于世界领先水平;坚持先进的环境保护理念,保证了经济发展与社会、环境的协调统一。
目前,中国石化与美国埃克森美孚公司和沙特阿美公司合资建设的福建炼化80万吨炼油乙烯一体化项目正在按照“世界级、高科技、一体化”的标准加紧建设。
规模从小到大,技术从无到有,乙烯生产基地的布局也从分散向沿海消费市场集中,一幅科学、合理的乙烯产业布局图逐渐成形。
在美国、日本等发达国家,乙烯建设中布局倾向于集中。美国乙烯生产能力多集中在墨西哥湾沿岸,日本集中在东京湾地区。在完成规模化改造和技术升级的同时,中国石化开始注重合理布局新增乙烯生产能力。
今天,在中国地图上,如果对中国石化的乙烯生产基地进行标注,会发现几大基地南北呼应,成为点缀在东部沿海的璀璨明珠。
在长江三角洲、珠江三角洲和环渤海湾地区,中国石化三个特大型石油化工产业基地群已初步形成,在这里建成了上海石化、扬子石化、茂名石化三个百万吨级和燕山石化、齐鲁石化两个80万吨级的乙烯生产基地。
同时,福建炼化、天津石化、镇海炼化等一体化基地的百万吨乙烯项目也在建设之中。
根据国家发改委2006年公布的《乙烯工业中长期发展专项规划》,乙烯工业的布局原则是加快沿海地区发展,统筹兼顾中西部地区。并提出,到2010年长三角、环渤海和珠三角三大乙烯产业区的产能要占到全国60%以上。
中国石化的乙烯生产布局,沿着科学合理的方向发展。
在每个乙烯生产基地,乙烯生产带动了塑料深加工、橡胶制品、纺织、石蜡深加工、助剂加工、包装材料、建设材料、化工机械制造、工程建筑、运输、餐饮服务等配套产业发展。一个百万吨乙烯项目,除本身直接提供一定数量的就业岗位、发挥巨大效益外,通过发展配套产品和深加工产品,初步测算可增加就业岗位15万个。
我国的乙烯工业在阔步向前,但发展中的差距仍在。据预测,如果国民经济继续保持7%-8%的增长速度,到2010年,我国乙烯当量需求量将达到2500万吨,而全国预计的实际产能将为1450万吨。同时,中东快速增长的乙烯产业,以其产品的低成本也将对国产乙烯产品市场形成冲击,中国乙烯工业发展任重道远。
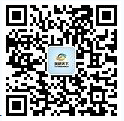
【版权提示】观研报告网倡导尊重与保护知识产权。未经许可,任何人不得复制、转载、或以其他方式使用本网站的内容。如发现本站文章存在版权问题,烦请提供版权疑问、身份证明、版权证明、联系方式等发邮件至kf@chinabaogao.com,我们将及时沟通与处理。