“目前3D打印已经实现了多个方面的突破。人造耳朵可帮助我国67万儿童摆脱耳朵不完全带来的困扰。人造骨骼、人造肌肉组织甚至是人造细胞都将在不久的将来得到应用。”国家先进成形制造教育部重点实验室副主任、清华大学机械工程系副主任林峰日前在中国科协科学技术传播中心及北京市科协共同主办、中关村天合科技成果转化促进中心承办的“产业前沿技术大讲堂”3D打印及增材制造技术及其产业应用专场做主题报告时透露。
突破传统制造“天花板” 让设计想象走进现实
林峰介绍说,作为一项新技术,3D打印技术将传统制造中的“切削”工艺变为“堆积”工艺,可以在产品内部不同位置放置不同的材料,该技术不仅具有数字制造、降维制造、堆积制造、直接制造和快速制造的技术特征,并在复杂结构的造型方面还具有独特优势。人造耳朵就是3D打印领域一个典型案例。
“通过计算机构建健康外耳的模型,并通过镜像得到目标外耳的模型,然后通过3D打印机,用特殊的材料打印出外耳,进而移植到患者耳部。这种技术不仅能保证再造耳与健康外耳形状对称,还能使患者免去传统手术造成的疤痕之痛。”林峰说。
不仅如此,3D打印还能完成在现实生活中许多运用传统加工技术难以完成的结构造型,且制造过程中不会出现材料浪费的现象。对此,受邀参加此次产业技术大讲堂的全国3D大赛组委会副主任兼秘书长、3D动力集团总裁鲁君尚深有感触:“此前设计师在设计零件时,要考虑工艺性。一些设计科班出身的毕业生步入工作岗位后,之所以常被车间的师傅笑话,原因在于其设计作品虽然很好,但却不具备可制造性,也就是说他没考虑工艺性。而3D打印不仅释放了设计师的灵感,也让更多不懂制造的人加入到了制造的行列。”
能做一些传统工艺难以做到的“奇形怪状”的结构只是3D打印应用的“冰山一角”。目前,3D打印技术已在航空航天等领域得到了初步应用。2016年2月,工业和信息化部、财政部等印发《国家增材制造产业发展推进计划(2015-2016年),明确将增材制造作为航空航天制造等高端装备制造及修复的重要技术手段。
航天一院总体设计部箭体结构设计室副主任(高级工程师)王婧超在此次大讲堂讨论环节中介绍说,火箭结构这类飞行器、运行器的重量很大,如果能在不影响其功能的前提下减轻其重量,将对增加有效载荷起到很大的贡献,可实现运载更多的东西进入太空。基于这样的考虑,长征五号在研制过程中首次全面采用了先进的数字化设计,开创了火箭型号数字化研制的先河,其主承力构件钛合金芯级捆绑支座就是3D打印出来的,它的强度不但不比用传统方法制造出来的高强钢支座低,反而更高,而且重量减轻30%,加工速度也更快。
根植行业细分领域 技术瓶颈待突破
“航空航天领域的3D打印应用正热火朝天,但很多技术在实际应用中仍是摸着石头过河。有的零件可以用3D打印,但零件所处的温度和运动条件一旦变了,就不一定行了。”王婧超坦言。
除了核心技术有待突破外,3D打印材料短缺也是制约该技术发展的重要瓶颈之一。据了解,目前增材制造的材料仅100多种,而传统减材制造、等材制造的材料有数万种。其次,材料的性能还不够稳定,且材料的通用性比较差、成本高企,这些制约着3D打印在工业领域应用的进一步发展。
据鲁君尚介绍,以目前在3D打印工业应用中使用最多的钛合金材料为例,其1千克的价格为2000-3000元左右。这意味着做一个20多千克的零件要花5、6万元,而传统铸造业只需几百元就能搞定,这使得3D打印在“高精尖”以外的其他工业领域难以推广开来。同时,材料的丰富性问题也是其团队在实践中遇到的困难。不少材料难以做到工业需求的抗疲劳和高温耐久等特性,很多应用施展不开。
此外,业内对3D打印材料的投入还不够,材料市场尚未形成充分竞争。不少3D打印巨头又做设备又做材料,材料与设备捆绑式销售,相对封闭的系统导致成本难以降下来。
对此,参加此次大讲堂讨论的天使百人会合伙人周洛宏表示十分关注。他说:“设备核心部件有没有突破,3D打印材料是不是高质量、低成本,制造工艺有没有创新等因素依旧是投资人最为关注的话题。”
周洛宏进一步解释说,目前3D打印在经历了前几年的市场追捧后渐趋冷却,甚至进入“寒冬”。据了解,2013-2015年,3D打印一度成为学术界、产业界争相关注的焦点,吸引了一大批跨界资本闻风而至,纷纷涉足项目、设备和应用投资。然而,短暂的繁荣表象的背后,3D打印却遭遇了装备及核心器件、成形材料、工艺及软件等产业基础薄弱、关键核心技术有待突破等一系列“成长的烦恼”,以至于在刚刚过去的2016年一年中,资本追逐一度冷却,出现了“叫好不叫座”的现象。究其原因,一是产品精度不尽如人意。影响产品精度的因素有很多,比如打印机本身的精度,打印过程中工艺参数的设定等。二是打印成本太高。目前,国内3D打印技术并不成熟,3D打印设备的核心部件、材料等仍然受制于国外,导致采购成本大幅提高。三是目前跨界资本纷纷涉足3D打印领域,导致市场上的3D打印设备、项目和市场应用鱼龙混杂。
“现阶段,3D打印主要解决的是生产发展中的刚性需求问题,那种利用3D打印制造一切的做法,我认为并不明智。未来3D打印的方向必然是按照行业细分领域深入发展,只要扎根设备、设计、材料、工艺等任何一个分支,将其做大做强,都会赢得市场。”鲁君尚说。
产业前景广阔 可与传统制造互为补充
有鉴于国内3D打印产业面临的种种瓶颈,此前出台的《“十三五”国家战略性新兴产业发展规划》明确提出,“十三五”期间,我国将从突破钛合金、高强合金钢、高温合金、耐高温高强度工程塑料等增材制造专用材料;搭建增材制造工艺技术研发平台,提升工艺技术水平;研制推广使用激光、电子束、离子束及其他能源驱动的主流增材制造工艺装备;加快研制高功率光纤激光器、扫描振镜、动态聚焦镜及高性能电子枪等配套核心器件和嵌入式软件系统,建立增材制造标准体系等方面着手推动3D打印产业的发展。
林峰表示,3D打印技术未来有着广阔的发展空间,例如一是应用于航空航天领域的功能部件直接制造,尤其是高性能金属零件的制造。二是应用于生物材料和活细胞的三维打印。这样一来就可在患者用药前,先把感染细胞抽出来培养,然后打印出来,用打印出的感染细胞试药,实现个性化治疗。三是应用于艺术创造的三维打印,比如服饰、建筑等。四是实现个人家庭桌边三维打印。
“尽管发展空间广阔,但是,3D打印并不能够替代传统制造,其发展方向应该是与传统技术相结合,互为补充。”林峰认为,3D打印与传统铸造技术的结合,能补足3D打印韧性不足、易断裂的缺陷。但在重型、大型装备制造方面,3D打印能推动大项目更有效率的进行。”
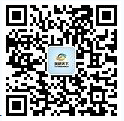
【版权提示】观研报告网倡导尊重与保护知识产权。未经许可,任何人不得复制、转载、或以其他方式使用本网站的内容。如发现本站文章存在版权问题,烦请提供版权疑问、身份证明、版权证明、联系方式等发邮件至kf@chinabaogao.com,我们将及时沟通与处理。