本报讯:
由于我国对机械基础件机械工业重要地位认识较晚,长期缺乏投入,致使整个行业基础差、底子薄、实力弱。特别随着我国主机水平提高,机械基础件落后于主机瓶颈现象日益显现。近年来,虽然技术引进、技术改造、科研开发等方面,国家给予了一定支持,但与当前市场需求及国外水平相比,仍有不小差距,具体表现:产品品种少、水平低,质量不稳定,早期故障率高,可靠性差。
我国机械基础件产品品种、规格少,特别高档产品差距较大,不能满足主机日益发展需求。目前,各类主机基础件性能指标大体相当于国外20世纪80年代水平。质量不稳定,早期故障率高,可靠性差,基础件致命弱点。因此,不少主机厂为提高其主机市场竞争力,往往选择进口基础件配套,致使国产基础件,特别技术含量较低产品,国内市场占有率有所下降。虽然我国基础件产品出口有明显优势,但主要劳动密集型产品,数量大,价值低,技术附加值不高。
当前,我国机械基础件行业存以下主要问题:
一重复建设严重,专业化程度低,形不成规模,经济效益差
机械基础件与主机相比,企业建立初始资金技术所需投入相对较少,因此国家几次经济大发展时期,都增加了一批基础件生产企业,随之也出现了大量低水平重复建设,点多、批量小,形不成经济规模。基础件企业虽然逐渐独立于主机厂,但大多数企业本身就大而全、小而全,专业化程度低,装备水平不高,质量不稳定,经济效益低下。如我国轴承行业三家大型骨干企业年产轴承总还不到国外一家著名公司50%。近两年,我国建成近百家液压件厂,但年产30万件以上只有几家,主要产品为农机配套。而德国力士乐公司年产各种液压件产品130万件,日本油研(株)也年产60万件以上。工业发达国家模具企业人均产值约15万~20万美元,我国只有4万~5万元人民币。近年来,随着多种所有制共同发展政策落实,基础件行业正经历着由分散到逐渐集集约化发展过程。
二科研开发力量薄弱,资金投入不足,技术进步缓慢
基础件各行业20世纪70年代末、80年代初就较早地引进了一批国外先进技术,但对消化吸收缺乏足够软硬件投入。据国外经验,引进技术与消化吸收所需资金比例约为1:7,而我国对此认识较晚,消化吸收步子较慢。市场竞争实际上技术实力较量。国外对此极为重视,纷纷加大投入,占领技术制高点。各大著名公司用于科研开发资金均占其销售额4%~5%,重点领域达10%。目前我国虽然有不少高等院校从事科研工作,不少理论研究、科研成果、专利论文均有相当高水平,但与生产实际结合不紧,特别转化成商品速度慢。
三原材料及相关技术落后,工艺及工艺装备水平低,制约了基础件发展
紧固件、链条、弹簧、轴承、模具等产品所使用钢材质量差、品种规格少,直接影响了基础件产品质量,而液压件铸件以及与液压件产品质量相关电控技术落后,也直接影响液压件质量可靠性。机械基础件一般都成批、大量生产,也有多品种、加工精度要求高产品,因此对生产工艺及其装备要求高,投资大。国外多采用高效高精度专机、生产线或柔性线,实现高效自动化生产。但我国一些基础件企业受资金制约,投入力度不大,企业自我改造能力差,先进设备少又不配套,影响了产品上质量上档次。
综合分析,造成上述问题主要原因于:
1.企业基础薄弱
由于我国机械基础件行业基础差,底子薄,科技投入少,开发力量薄弱,不能适应主机行业引进、合资、合作、快速发展需要,导致机械基础件国内市场占有率有所下降。
2.国家缺乏对机械基础件行业有力政策支持
虽然国家产业政策方面,明确了重点支持重要机械基础件(模具、轴承、液压、气动、密封件等),但缺少相应配套政策支持,如模具行业税负过重,享受增值税部分返还企业,全国只有不到百家,面太窄,作用有限,还需要政策继续支持等。
因此,为提高我国机械基础件产品市场竞争能力,更好地满足我国机械工业对国产基础件配套需求,预计我国基础件行业面临进一步调整,以整合优势资源,淘汰落后企业。今后5~10年,行业将发展品牌产品及名牌企业、开展技术创新、提高国内外市场竞争能力加强集约化经营等方面力争有较大进展突破。
五金基础件行业存在的问题分析。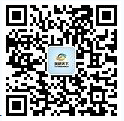
【版权提示】观研报告网倡导尊重与保护知识产权。未经许可,任何人不得复制、转载、或以其他方式使用本网站的内容。如发现本站文章存在版权问题,烦请提供版权疑问、身份证明、版权证明、联系方式等发邮件至kf@chinabaogao.com,我们将及时沟通与处理。