本报讯:
长期以来我国重主机、轻配套的发展思路,致使大型铸锻件,以及液压件、密封件等基础零件一直成为制约我国大型成套设备发展的瓶颈。“这些部件看起来不大,但其经济效益比较可观,而且具有很强的战略意义。”提及前不久出台的装备制造业调整振兴规划,第一重型机械集团公司董事长吴生富颇为感慨。他表示,“希望规划能进一步细化、落实,同时尽快建立完善的机制,对大型铸锻件的技术水平提升起到实实在在的促进作用。”
工业和信息化部一内部人士向本报记者透露,关于提高我国大型铸锻件自主化的细则正在研究中,不久后将出台。
大型高端铸锻件欠缺
近年来国家不断加大重大装备的国产化力度。一重、二重、太重、中信重工等大型铸锻件企业也纷纷投入巨资开展技术攻关,提升大型铸锻件尤其是核电锻件的技术水平和生产能力,目前我国已形成了大型铸锻件和反应堆压力容器制造基地。
继一重集团建成1.5万吨自由锻造水压机、二重集团研制成功1.6万吨自由锻造水压机后,上重的1.65万吨自由锻油压机和中信重工的1.85万吨油压机也在积极建设中。尤其是中信重工的1.85万吨油压机无论是规格还是技术,目前在世界范围内都是惟一的。万吨油压机等高端设备的陆续出现,势必对世界重大装备制造业产业格局产生影响。
“尽管我国的装备能力已远远超过日本制钢所和法国的布鲁梭,但一些大型高端铸锻件尚未形成产能,产品技术尚不能支撑市场需求。”业内人士表示。
“在核岛与超超临界百万千瓦级火电机组中,一些超大型锻件和特殊材料、特殊结构的大型电站铸锻件等依旧短缺,满足不了国内市场需求,特别是一些高质量、高要求的大型铸锻件国内目前还供应不了,比如超超临界百万千瓦、60万千瓦的挤压装置。”中国重型机械工业协会名誉理事长汪建业认为。
据介绍,以千吨级以上热壁加氢反应器为代表的大型压力容器锻件,以半组合曲轴、尾轴及舵杆为代表的大型船用铸锻件,以5500毫米宽厚板轧机支承辊为代表的单重百吨级以上大型支承辊锻件及以高速钢轧辊为代表的特殊材料轧辊锻件等也亟待提高自主化制造能力。而与此同时,百万千瓦级核电机组常规岛低压整体转子锻件还依旧依赖进口。
“我国一些大型铸锻件仅处于试制阶段,从制造到应用于项目上,还有一段距离。”采访中,中广核一内部人士不无担忧地说,我国的核电建设已进入快速发展期,“迫切的市场需求给大型铸锻件制造企业带来了很大压力。如何保证质量以及按时交货将是一个很严峻的问题。”
冰冻三尺非一日之寒“冰冻三尺非一日之寒”.在提及我国大型铸锻件国产化难题时,不少被访者都有此感慨,“这是行业多年来存在的问题,比较复杂。”
“我认为还是体制问题。”汪建业表示,“我国重型机械制造厂基本上都有自己的大型铸锻件生产分部,致使大型铸锻件生产并未完全进入市场竞争,一些企业基本依靠其母体公司,其效能并没有完全发挥出来。三个基地的总产量还赶不上日本的一个企业。这说明产能没能很好地规划。”
至于高端产品研制难,汪建业认为还是缘于成套能力不足。“比如,目前我们的大型铸锻件还需要大吊车吊起来,这导致效率的低下。部分企业的油压机、水压机与旁边的操作机并不匹配,结果设备虽好,但却没能发挥应有的作用。”
“这还与以往重视程度不够、研发投入太少有关系。”汪建业指出,“自上世纪八十年代以来,一些研发经费完全依靠国家投资,投资不到位研发就难以进行。国家应成立一个专家组,认真研究行业发展的症结所在,究竟缺什么?到底需要多少资金?然后根据认证结果进行整体的规划部署。”
中国机械工业联合会副会长蔡惟慈也表示:“目前我国设备已经非常先进,差距还在软件上。大型铸锻件在大型火力、水力、核电、大型轴承锻件等方面的问题还没完全解决。热加工要比冷加工难得多,它还包括长久积淀的经验、工艺等那些看不到、摸不到的技术。与世界水平相比,我们还欠缺很多。”
“我们还缺乏技术以及能让这些设备真正发挥出优势的人才。”中国重型机械工业协会副总工程师傅树利强调。
细则将出各方献策2月4日国务院审议并原则通过了装备制造业调整振兴规划,提出“要提升大型铸锻件、基础部件、加工辅具、特种原材料等配套产品的技术水平,夯实产业发展基础”.“现在国家充分支持我国大型铸锻件发展,希望整个行业能充分把握这次难得的机遇。”傅树利表示。
要提升大型铸锻件的技术水平,汪建业认为,大型铸锻件生产应尽快从母体公司中彻底分离出来,直接面对市场的考验。这样,才有可能通过政策引导和资金支持对大型铸锻件生产单位进行兼并重组,逐步形成具有国际竞争能力的大型铸锻件企业集团。
目前我国已研发出万吨油压机等世界尖端设备,当务之急是尽快形成完善的配套能力。“如配套必要的大型铸锻件科研手段,配套锻造过程中大锻件非接触尺寸测量装置等,这些测量设备及工装、辅具对大锻件锻造质量及锻造效率有着决定性的影响。”有专家建议。
“当前解决我国大型铸锻件瓶颈问题的关键是强化对基础工艺技术和共性技术研究的支持力度。”在向工信部装备司提交的《关于提高我国大型铸锻件自主化能力的建议的报告》中,中国重型机械工业协会表示,“应尽快制定可靠的大型铸锻件制造工艺参数,真正使大型铸锻件的生产从’必然王国‘走向’自由王国‘,从而减少投料废品损失。为此,建议尽快建立国家级大型铸锻件共性技术研究室,并明确大型铸锻件科研攻关经费的专项申请渠道。”
此外,也有企业表示,“大型铸锻件尤其是百万千瓦级核电大型铸锻件的科研攻关难度大、周期长、需求急,存在着很大的首件投料失败风险,而这种投料失败损失要高达几百万元甚至上千万元,仅由投料企业承担不尽合理,希望国家能建立大型铸锻件首件投料风险补偿基金。
一重一内部人士表示,现在国内核电装备制造存在着法国和美国两套标准,”这给制造企业带来了很大麻烦,每个业主都有自己的标准,这无形中增加了设备国产化的难度。“他表示,制造企业迫切希望能尽快统一核电装备标准,并且能与设计院、业主等一起参与到设备设计、制造等相关标准的制定中。”
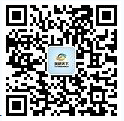
【版权提示】观研报告网倡导尊重与保护知识产权。未经许可,任何人不得复制、转载、或以其他方式使用本网站的内容。如发现本站文章存在版权问题,烦请提供版权疑问、身份证明、版权证明、联系方式等发邮件至kf@chinabaogao.com,我们将及时沟通与处理。